【導入事例】Vestas社:Direct Digital Manufacturingを導入して企業競争力アップ
- 3Dプリンター
- 2024.3.6
- Markforged 導入事例 X7
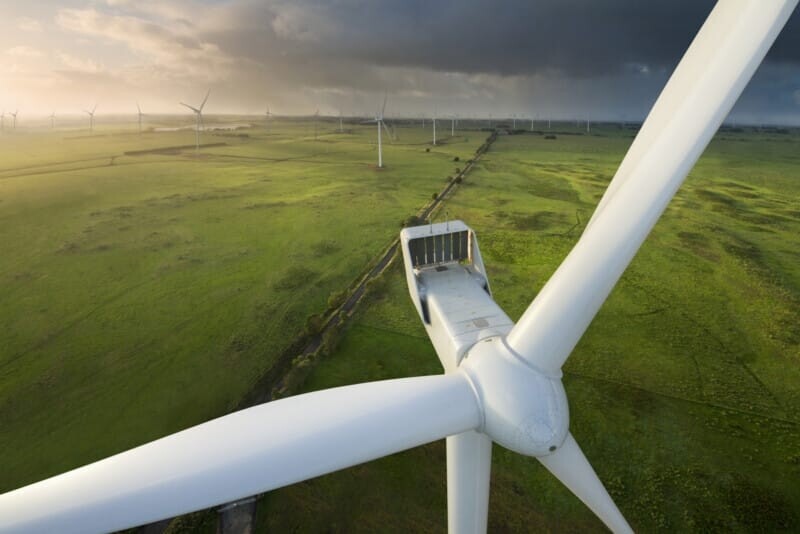
Vestas社は世界86カ国で合計151ギガワット以上の風力タービンを設置しており、競合他社を圧倒しています。
カナダの調査会社Corporate Knights社の独自調査「Global100(2022年度)」では、持続可能な社会に最も貢献している企業として名前が挙げられました。同社は、2030年までにネットゼロ脱炭素化を実現すること、2040年までに廃棄物ゼロの風力タービンを製造することを経営戦略に掲げており、アディティブ・マニュファクチャリングを採用し始めました。
今回はアディティブ・マニュファクチャリングを活用したVestas社の経営戦略をご紹介します。
Vestas社とは
Vestas社は、化石燃料に変わる代替エネルギーの風力を作り出す風力タービンを製造・設置している企業で、風力エネルギー業界ではグローバルリーダー企業として知られています。
風力タービンは高さ137m~259m(450-850 ft)、ローター・ブレードの直径109m~236 m(360-774 ft)と大型の装置です。遠く離れた場所からも風力タービンが見えることがあります。もし風力タービンを見たことがあるなら、それはVestas社が製造した可能性が高いです。
Vestas社の歴史
Vestas社は、第二次世界大戦後のデンマークで家族経営のメーカーとして誕生しました。当時は軽トラックの油圧関連装置を製造、販売していました。
1970年頃から代替エネルギーに着手して、1979年に初の商業用風力タービンを完成させました。1989年から風力タービンの製造・販売に特化して「設計」「製造」「設置」サービスを提供しています。
そして、現在は陸上および洋上の風力タービンおよび風力タービンブレードの世界最大のメーカーです。会社はデンマークに本社を構え、いくつかの地域オフィスと、世界各地に15以上の製造工場を持っています。
Vestas社の挑戦
風力タービンは高額で大型装置であるため、風力エネルギーを効率よく作るためにダウンタイムを最小限に抑える必要があります。そのため、製造や設置時においてミスが許されません。製造現場や設置現場では多数のゲージ検査が行われています。ゲージ検査に使うツールは、製造指示書に従って、世界中のベンダー企業から調達し、風力タービンの最終部品としては、ゲージ検査に合格したものを使用しています。しかし、メーカーから供給された部品の中には検査に合格しないものも含まれており、この問題により製品の納品や設置が遅れていました。
調達部品の納期の問題
部品は専門的な検査プロセスを通過したとしても、多くは時間がかかりコストが高い従来の加工方法と原材料で製造されていました。
例えば、トップセンター(TC)マーキングツールを考えてみましょう。これらの重要なツールは、Vestas社がタービンブレードの根元をマークしてピッチを合わせるために使用され、通常約5週間かかって製造されます。さらに、あらゆるブレードに適合するようにTCマーキングツールの複数のバージョンを注文しなければなりませんでした。
また、落雷による被害を軽減するための雷受容器はアルミニウムでのサブトラクティブ工法(減算製造法)で製造するため、発注から納期まで最低12週間かかっていました。

アディティブ・マニュファクチャリングの主任エンジニアであるJeremy Haight 氏は「Vestasは、中央集権的なエンジニアリング制御モデルを維持しながら、製造をエンドユーザーの手に委ねることで、製造を民主化しています。」と述べています。
Vestas社の製造プロセスの見直し方
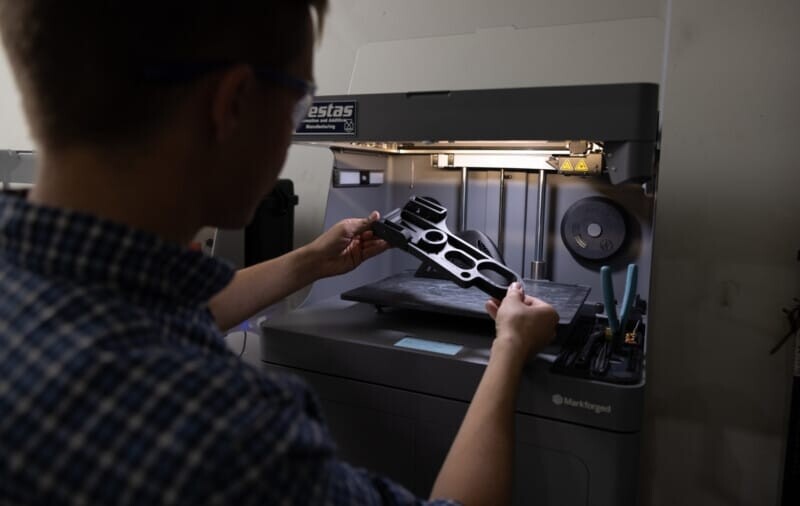
Vestas社は部品の納期の問題を解決するために製造プロセスを根本的に見直しました。
2021年にMarkforged社のクラウドベースのAI駆動のDigital Forge付加製造プラットフォームを使用してDirect Digital Manufacturing(以下「DDM」という)プログラムを立ち上げました。これにより、社内であらゆる部品を製造できる体制を整えて、外部サプライヤーに依存しない製造工程を実現しました。また、協力や連携のための情報や知識を共有するプラットフォームを提供しており、外部サプライヤーとコラボレーションするためにノウハウをデータベース化しています。
製造ノウハウを共有
DDMを実現するために、Markforged Eiger™クラウドベースのデジタルリポジトリに2000以上のVestas社の部品を保存しています。
デジタルリポジトリに登録しておくことで、3Dプリンターに関する知識が全くない方でも部品を製造することが可能です。Vestas社ではMarkforgedの3Dプリンター「X7」で繊維強化複合部品を造形し、3Dプリンター「Onyx One」で複合部品を造形することができます。
主任エンジニアのJeremy Haight 氏は「私たちの取り組みは一貫しており、ほぼリアルタイムで製品をさまざまな場所に届けることができます。これは、瞬時に物を移動させるテレポーテーションに近いものだと感じています。」と述べています。
リポジトリのおかげで、Vestasのチームは世界中のどこでも、専門家の必要なく、瞬時に一貫して仕様通りの部品を得ることができると確信しています。
リードタイム短縮やコスト削減に成功
DDMにより、部品製造のリードタイム短縮やコスト削減に成功しました。
例えば、発注から納期まで5週間かかっていたセンターマーキングツールは数日で作れるようになりました。それだけでなく、このセンターマーキングツールを作る際に繊維強化オニキス、耐久性のある軽量なナイロンブレンド材料を使用して印刷するため、以前の金属部品に比べて85%軽くなっています。
また、雷受容器は、地元のブレード製造サイトで銅を用いて3Dプリント技術で製造されます。Vestasは、一度導入されれば、各受容器の製造に約2日かかると見積もっています。特筆すべきは、Vestasのチームがこれらの部品や他の部品に関して、コンプライアンステストの合格を心配する必要がない点です。
なぜなら、これらの部品は正確なデジタル仕様に基づき、オンデマンドで社内で印刷されるからです。さらに、ツールの精度はMarkforged Blacksmith™を使用して、製造過程での検査、分析、報告が行われています。
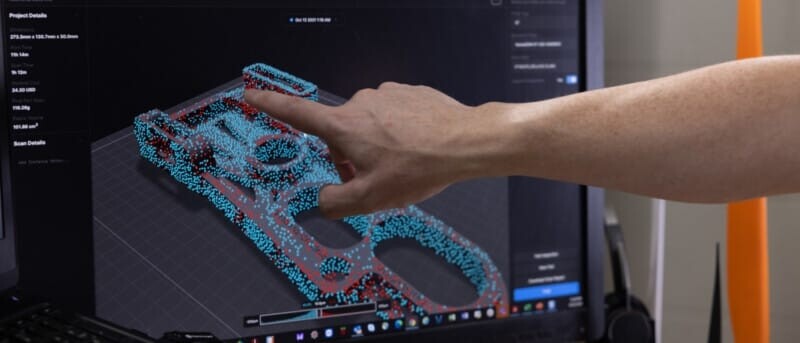
Blacksmithのデジタル部品検査は、TCマーキングツールの印刷精度を確認します。主任エンジニアのJeremy Haight 氏は「私たちはMarkforgedを選択しました。なぜなら、彼らがDDMのビジョンを実現するために必要なエンドツーエンドのソリューションを最も適切に提供できるからです。」と述べています。
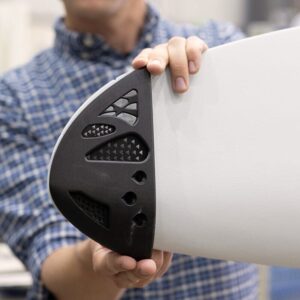
Vestas社の将来
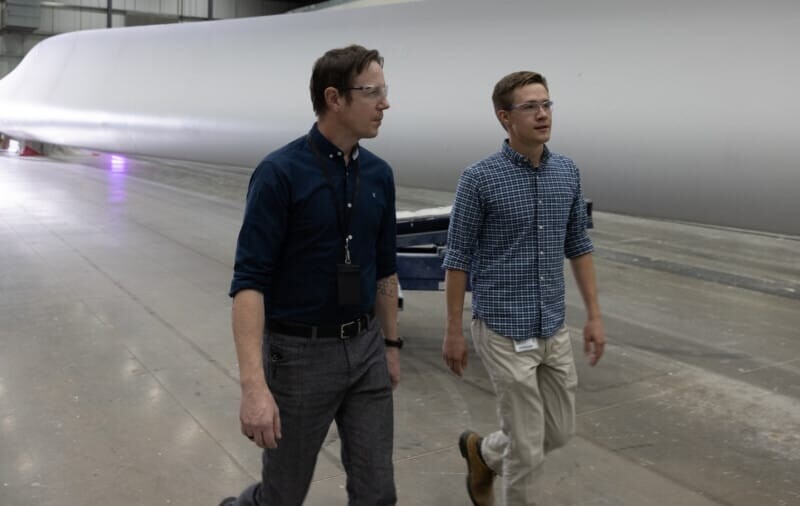
VestasのAMチームのメンバーは、ツールや最終使用部品の品質と性能を確保するための取り組みを主導しています。
Vestas社は新製品の開発やツール、最終製品の部品の供給性において、DDMを事業全体での重要な要素と見ています。2022年に、同社はブレードを超えた検査ゲージツーリングのためのDDMの展開を開始し、23ヶ所の製造拠点すべてでオンデマンドのゲージ生産を促進する予定です。
またVestas社はWürthと業務提携し、地域のフィールドサポートや他のサプライヤーのための保守、修理、運用(MRO)をサポートするために、The Digital Forgeプラットフォームで作成されたスペアパーツの在庫を管理し、付加的なエコシステムを構築しています。初期の展開が完了すると、Vestasは各サイトでより深いエンドツーエンドのプロセスの実装に注力する予定です。
同社は、Vestasの各サイトで適切な権限を持つ者が、部品コードをスキャンするか、エンタープライズ資産管理(EAM)やエンタープライズリソースプランニング(ERP)システムで部品検索を容易にしています。検索された部品は自動的に対応するローカル3Dプリンターに送られます。
BlacksmithとEiger Fleet™を使用したユーザー、プリンター、部品検査の中央集権的な制御により、風力タービンのブレードの取り付けや調整を正確に行うための高品質で高性能なツールと部品を確保しています。
まとめ
エネルギー業界のグローバルリーダーVestas社は、不適合品による製造の遅延や製造コストを課題に感じていました。このような課題を解決するためにMarkforged社によるDDMプログラムを導入しました。
Vestas社が導入しているMarkforgedの3Dプリンターに興味を持った方は、APPLETREEのショールームにお越しください。ショールームではMarkforged社の3Dプリンターを直接体験いただけます。ショールームの予約をお待ちしております。