【導入事例】FESTO社:電子部品製造の革新的な生産性向上
- 3Dプリンター
- 2024.6.27
- Markforged 導入事例 X7
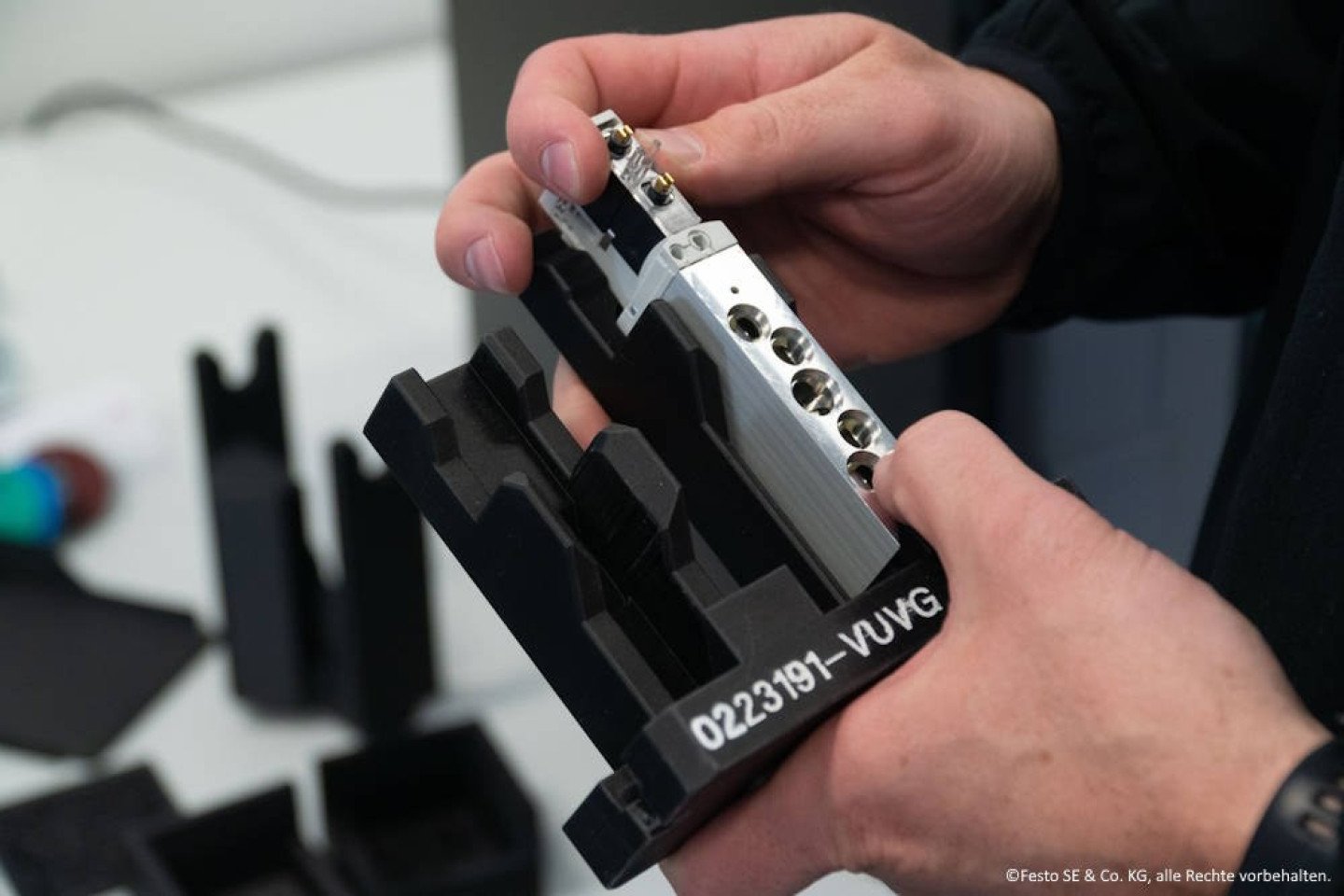
目次
FESTOとは
世界60カ国以上で20,000人以上の従業員を抱えるFESTOは、自動化技術のグローバルリーダーです。革新的な製品、卓越した品質、複雑な自動化技術と技術教育のソリューション提供で知られる同社。その中でも、シャルンハウゼン・テクノロジープラントは、バルブ、バルブターミナル、電子機器の主力工場として注目を集めています。
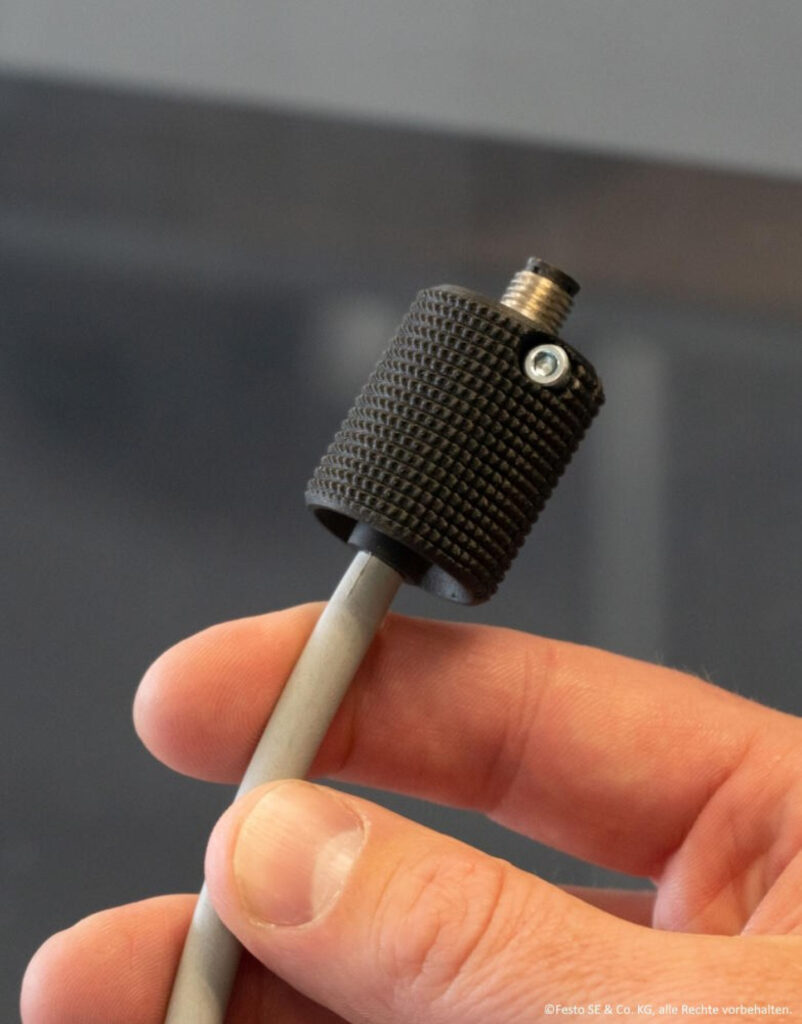
高度な個別機器への需要
2014年以来、シュトゥットガルト南部に位置するFESTOテクノロジー工場は、最先端の生産設備と高度に最適化された自動化プロセスを特徴としています。このハイテク機器や設備を効率的に運用するには、予期せぬダウンタイムを最小限に抑え、生産効率を維持するための多種多様な個別機器が不可欠です。高品質な予備部品や治具を使用することで、FESTOは高い生産品質と顧客満足度を確保しています。
ESD要件がもたらした課題
運用機器設計の責任者であるStefan Fent氏とそのチームは、単なる3Dプリンティングを超えたソリューションを求めていました。多様な機器の運用にかかる高コストと作業負荷の軽減が目標でした。彼らが求めていたのは、機械的に堅牢な部品を安全かつ再現性高く生産できる本格的な製造システムでした。
特に注目したのは、これまで機械加工や外部委託で製造していたプラスチックやアルミニウム製部品の代替でした。さらに、電子機器製造の厳しい要件を満たすESD(静電気放電)対応部品の安定生産も必須条件でした。
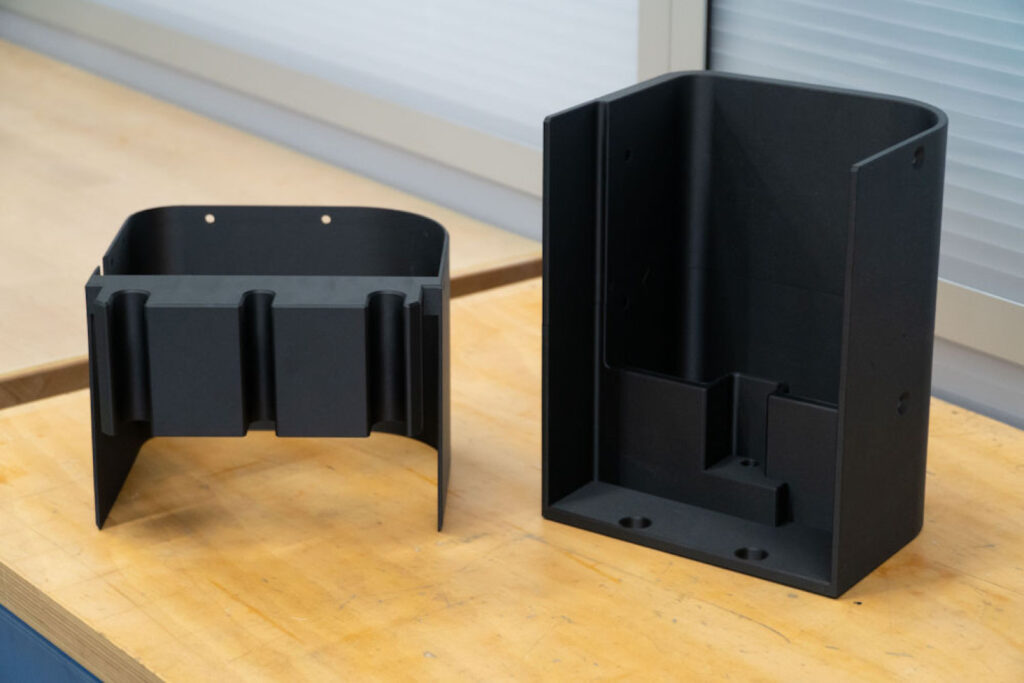
FESTOは以前にも3Dプリンティングの導入を試みましたが、ESD要件を満たせず断念した経緯がありました。多くの3Dプリンターが存在する中、業界標準を確実に満たすものは稀でした。しかし、Markforgedにとって、これは問題ではありませんでした。
ワンストップの産業用3D印刷ソリューション
地域の展示会で、チームはMarkforgedの付加製造機に出会いました。Markforgedの連続繊維強化技術により、機械的強度の問題はすぐに解決。連続炭素繊維を使用することで、アルミニウムを上回る強度さえ実現可能になりました。
Markforgedは、ソフトウェア、ハードウェア、材料が連携するようデザインされています。このエコシステムの各要素が目的に応じて構築されており、最高の信頼性とプロセスの安全性を提供します。
Markforged Onyx ESD材料は静電気散逸性を持ち、EMS業界の静電気対策要件を満たしています。
2022年春、Stefan Fent氏はMark3D – Markforgedの2台の製造機を生産設備に導入することを決定しました。それ以来、Markforged Onyx ProとMarkforged X7が24時間体制で治具やテンプレートを製造しています。Onyx Proはデスクトップマシンで、連続ガラス繊維強化部品の生産に適した万能機です。一方、Markforged X7は、連続炭素繊維、ガラス繊維、ケブラーを部品に挿入することで、機械的に強靭な部品を生産します。さらに、X7はOnyx ESD材料を使用して電子機器生産用の部品を印刷することができます。
FESTOの生産設備設計エンジニア、Johannes Hablizel氏は次のように述べています。「Markforgedは真の製造システムです。部品の品質と強度、そして信頼性が他の競合製品を凌駕していると確信しています。」
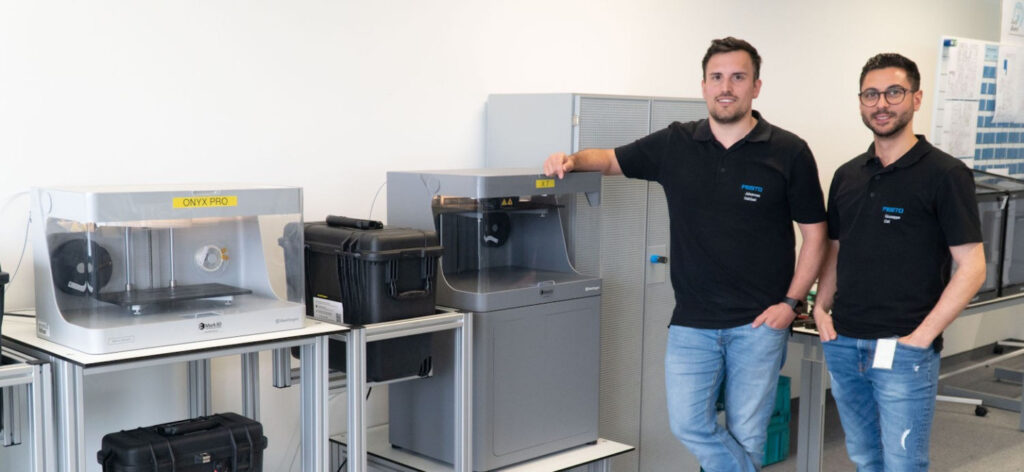
付加製造的思考への移行
設計者たちが3Dプリンティングを設備製造に組み込み始めるまでに約2〜3ヶ月かかりました。しかし、9ヶ月後の現在、プリンターはすでに数週間先まで予約で埋まっています。チームの学習曲線は指数関数的に成長しています。
製造機は社内の複数の従業員によって操作されています。付加製造された部品は、大小を問わず生産現場の様々な場所で見られます。センサーホルダー、ハウジング、ハンドル、クランプおよび保持装置、工具、テンプレート、予備部品などが含まれます。
FESTOはすでに200種類以上の部品を付加製造しており、これらは従来であれば高コストでミリング加工や外部発注が必要だったものです。
共有データベースにより、今後の印刷ジョブの概要、コストと節約額が把握でき、ジョブを効率的に処理するのに役立っています。
付加製造は今や、シャルンハウゼンのFESTOチームにとって確立された製造技術となっています。
9ヶ月で80,000ユーロ以上のコスト削減
受注データベースの分析により、印刷部品によるコスト削減効果も明らかになりました。様々な部門からの需要が急増したことで、設備設計部門のチームは9ヶ月間で約80,000ユーロの節約に成功しました。
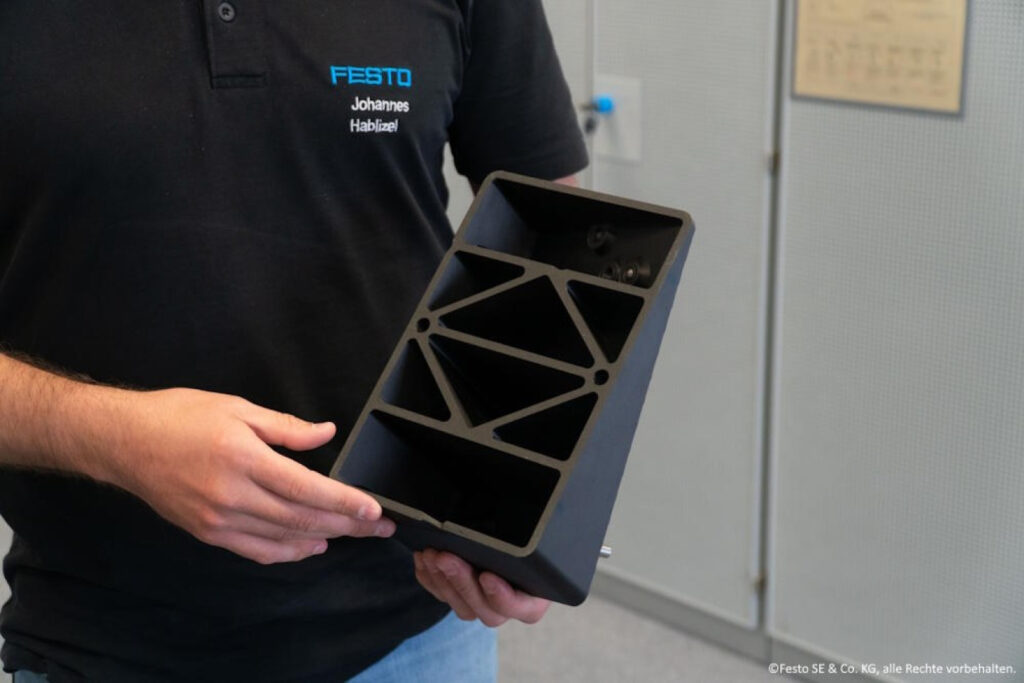
実例:ハンドヘルドESDスキャナーホルダー
コスト削減を示す好例が、シンプルな3ピース構造のハンドヘルドスキャナーホルダーです。従来の機械加工による生産では、10個あたりの見積もりコストは約4,000ユーロでした。3Dプリンティングを使用すると、Onyx ESD材料で作られたホルダーのコストはわずか385.88ユーロで、労務費200ユーロを加えても、機械加工と比較して3,414.12ユーロの節約を実現しました。
適材適所で使用すれば、3Dプリンティングはあらゆる企業に多大な付加価値をもたらします。
デジタルフォージ
FESTOで印刷された部品を見ると、各部品にシリアル番号や部品識別子が付いていることにすぐ気付きます。部品や組立品の一部が損傷したり摩耗したりした場合、交換部品を再印刷できます。
Markforgedのダイナミックな付加製造ソフトウェア「Eiger」を使用すれば、世界中のどの生産拠点でも、必要な部品をオンデマンドで製造できます。選ばれた従業員がデータにアクセスし、管理することができます。
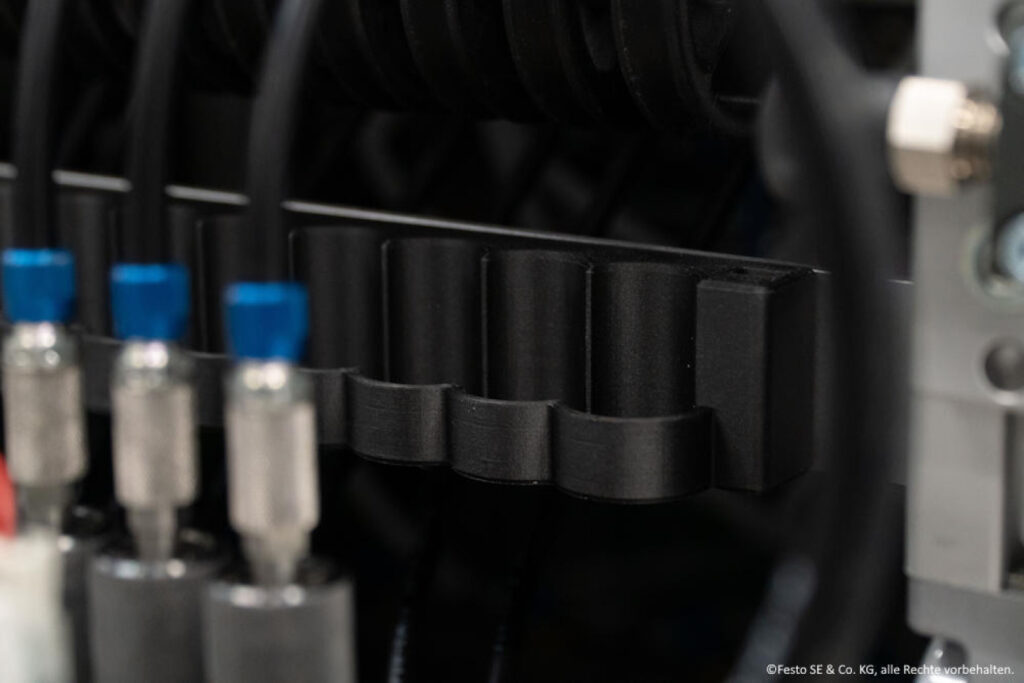
今後の展望
今後は、3Dプリンターの現在の稼働率を維持していく予定です。需要が増加し続ける場合は、ポートフォリオの拡大も検討されています。
さらに、新しいMarkforged FX20産業用3Dプリンターの潜在能力を評価中で、生産への導入可能性を検討しています。生産能力の向上と、さらに大型の部品製造が可能になれば、FX20はFESTOにとって新たな成功事例となる可能性があります。
まとめ
FESTOの事例は、適切な3Dプリンティング技術の導入が、製造業にいかに革新的な変化をもたらすかを示しています。
コスト削減、生産効率の向上、そして柔軟な製造能力の獲得 – これらの利点は、今後の製造業の未来を形作る重要な要素となるでしょう。